Most major OEMs have indeed taken eco-design approaches to reduce the environmental footprint of their packaging. Light weighting, replacement of materials with circular ones, packaging design so that they can be reused or recycled are just some of the efforts that have been made to reduce the environmental impact of packaging.
To replace plastic and zamak commonly used in Beauty packaging, aluminum is one of the materials of choice thanks to its better recyclability. But with traditional metal processing techniques, complex shapes and fine details made of metal are often shelved at the designer’s desk, rather than propagated to the shop floor. With its groundbreaking HPP forming techniques, Bmax offers a unique possibility to design and manufacture exclusive products made of aluminum while reducing environmental impacts.
Products manufactured by our systems
Our added value
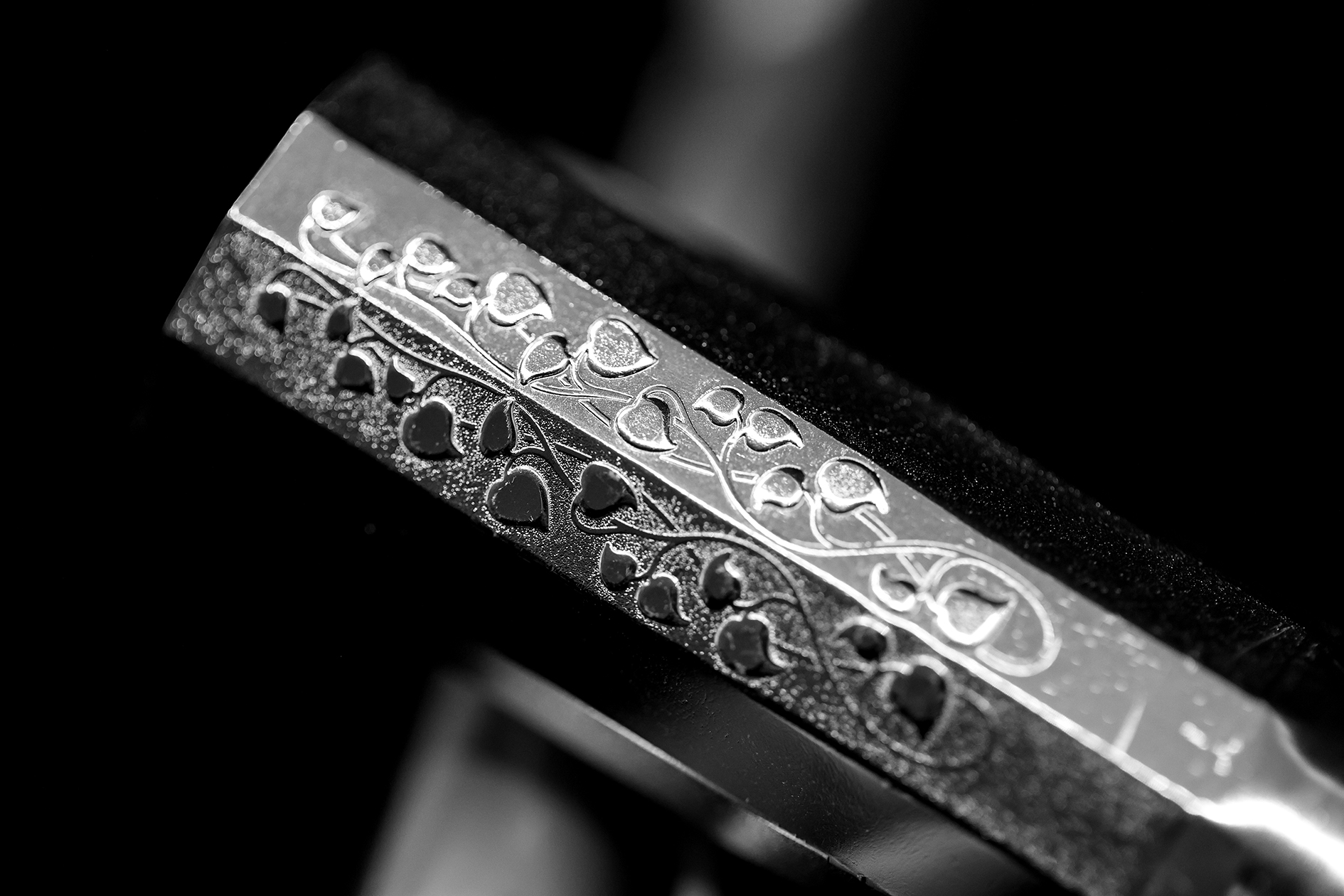
Exclusive, unique designs from aluminum and various materials with uncompromised esthetics: original texturing, engraving of very fine details, precise and refined lines and customer logos, forming of complex shapes
- Powerful numerical simulation tools for optimized co-engineering of products with Customers
- Proprietary assets for fast prototyping and qualification
- Mass production systems with full product lifetime experience
- Use of highly recyclable materials like aluminum, instead of plastic and zamak
- Possibility of thinner packaging by 20 to 50% (less CO2 footprint, material and cost savings), thanks to higher material formability
- Processes with very low energy consumption
- No polluting emissions, no use of chemicals
- Use of low quantities of water in closed circuit loops
- Made in France (less CO2 footprint due to transportation)
Are you interested?
Contact us