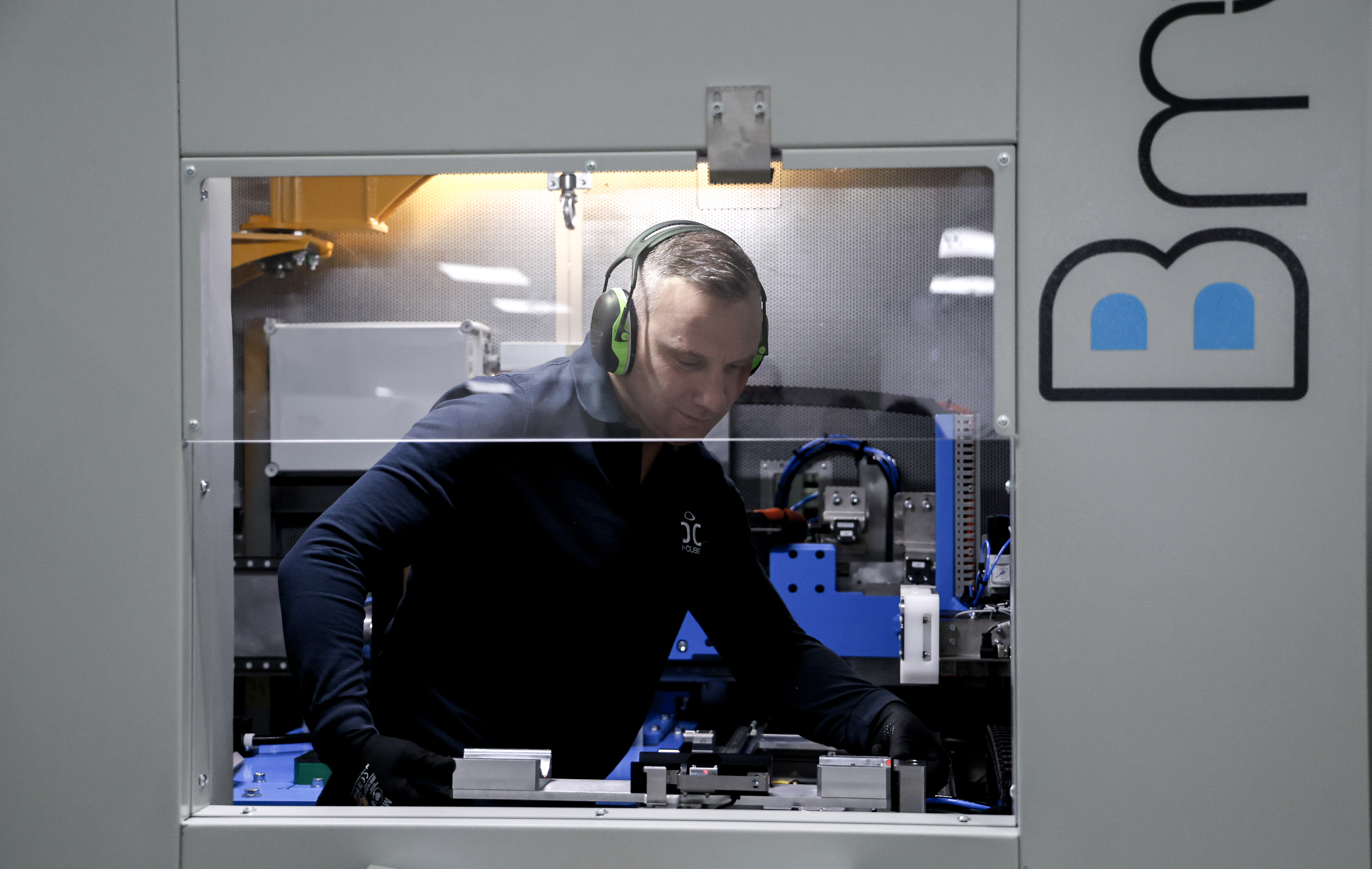
Increasingly efficient and reliable, our industrial, turnkey MPW systems are currently being used by automotive industry leaders for mass production of key components of highly efficient HVAC (Heat Ventilation & Air Conditioning) systems utilized in electric vehicles, like R744 (CO₂) accumulators and R290 (Propane) receiver driers.
We enable our customers to save material, resulting in weight and cost savings, while ensuring high levels of product performance.
Welding System
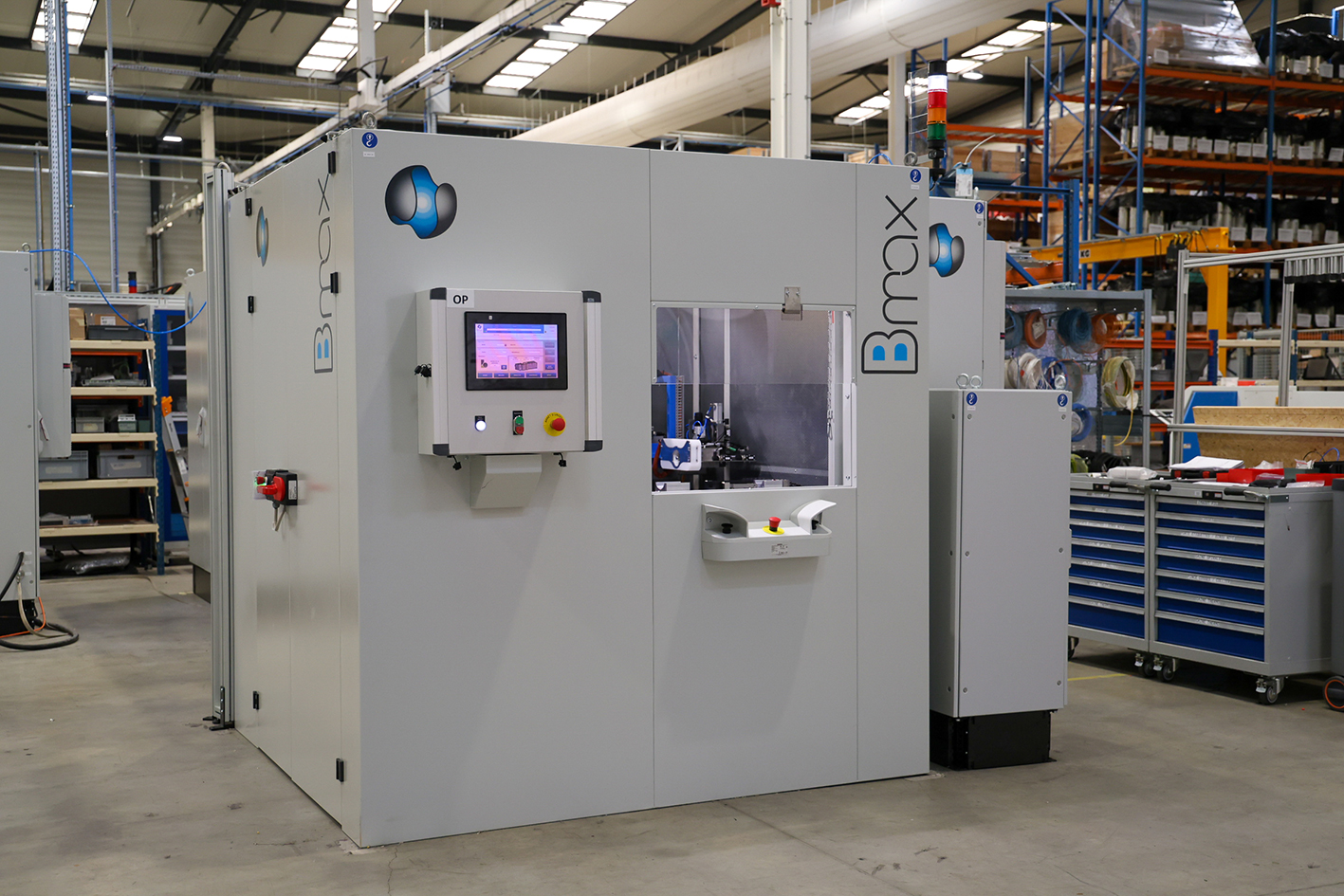
Tube to Cap type Pressure Vessels - e.g. R744 (CO2) Accumulators or R290 (Propane) receiver driers
Tube:
- Dimensions: up to ⌀100mm & 5mm thick – depending on material grade
- Material grade: Al 6xxx series as a standard – other material possible on demand
Cap:
Material grade: Al 6xxx series as a standard – other material possible on demand
- Embedded with the highest level of machine security in the market
- CE-certified with the support of an independent certification body
- Fully compliant with applicable regulations, technical standards and directives
- EMC and sound proof workstation
- Optimized footprint
- Production throughput: 1,000,000 welds/year
- ≥80% OEE (Overall Equipment Efficiency)
≤20 sec cycle time per weld, with no cooling downtime – Welding time ≤100µs
- Cpk>2
- No mechanical contact between tooling and parts to be welded
- Highly synchronized switches ensuring extremely low variations of electrical signals
- Scrap rate close to 0%
- Fully integrated Process Monitoring System with real time welding data acquisition & recording
- Real-time detection of defective weld
- Stand-alone, turnkey system, easy to install in any industrial environment
- User-friendly HMI
- Easy access to product positioning cart
- Secured access doors to perform maintenance operations
- Integrated lifting devices, enabling ergonomic, safe and easy maintenance
- ≤15min tool changeover time
- Remote assistance/maintenance capability
- Optional diagnosis function
- Low electrical power consumption <6kW (production mode)
- No filler material, no toxic fumes, no dangerous radiation
- No need for cleaning the parts, neither before nor after welding
download
Technical Brochure
Industrial, turnkey equipment for mass production of key components of highly efficient HVAC systems utilized in electric vehicles.
Premium Technology
Magnetic Pulse Welding | Conventional Welding | |
Welding Technology | Cold Welding, <br>No Heat-Affected Zone | Fusion Welding |
Weld Strength | No degradation of materials’ properties | Heat-Affected Zone inherently makes weak seams |
Weight Saving | >20% weight reduction | Extra material thickness required due to embrittlement of materials |
Dissimilar Materials | Wide range of materials combinations: Al/SS, Al/Cu, Al/St, etc. | Not possible |
Process Cleanliness & Simplicity | <center>-</center> | Pre/post treatments <br>Use of inert gas <br>Very precise positioning<br>Laser beam safeguarding<br>Special anti-radiation enclosure |
Scrap Rate | <0.1% | 3-5% |
Energy Consumption | < 6kW | >60% more consumption |
Consumables | <center>-</center> | Inert gas and a lot of other consumables are required |
Weld Quality & Aspect | Excellent quality, very aesthetic with no joint distortion | Joint deformation and distortion, due to heat and residual stress |
Different products manufactured by our systems
Other Solutions
Are you interested?
Contact us