Our proprietary field shapers crimp the terminal to the high voltage cable in under 100 microseconds. Thanks to the high deformation speed, MPC results in little to no residual forces that would lead to a relaxation of the crimp over time due to repeated thermal cycling. This is vital to high voltage wire harnesses. MPC delivers the most robust connection over lifetime testing, as the integrity of the crimp remains consistent from initial production to the end of the vehicle life, unlike a mechanical crimp.
Our one-stop shops in both the US and France are equipped to provide: rapid prototyping, high volume production, testing and extremely fast delivery times, for a wide range of wire sizes (up to 300mm2).
Products manufactured by our systems
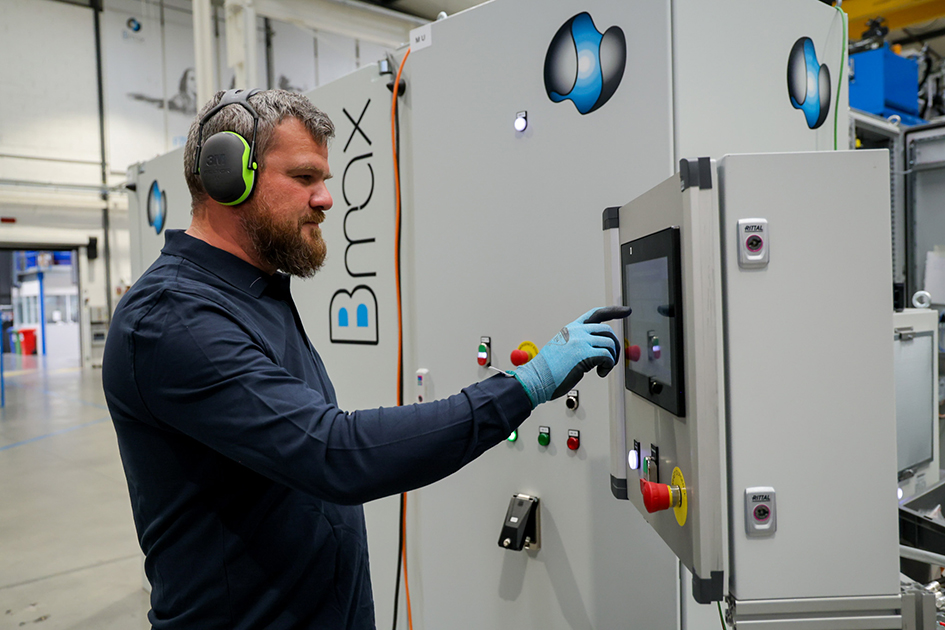
Bmax is the top choice for high voltage wire harness production. With our unmatched capacity, thanks to multiple MPC crimping systems and our in-house capabilities of simulation, micrography and hi-pot testing, we ensure an uninterrupted supply of serial production wire harnesses.
Quality is paramount, with ISO certification and 100% part traceability, ensuring the reliability of our products. We design and manufacture our own systems, maintaining a complete inventory of spare parts, allowing us to perform preventative maintenance and service in-house. With this integrated approach, our operations are seamless and we are able to consistently deliver high quality wire harnesses to you on time.
Premium Technology
Magnetic Pulse Crimping | Conventional Crimping | |
Electrical Resistance | Reduced resistance | Increased resistance |
Compression Rate | Higher compression eliminates air gaps between strands | Air gaps present with big cable sections |
Crimp Resistance & Durability | Improved tensile strength with minimal relaxation over time<br> Highest performance with vibration and pull force testing | Higher relaxation over time<br> Limited vibration and pull force resistances |
Materials Combinations | Use with dissimilar materials (e.g. Cu/Al, Cu/Cu, Al/Al, etc.) <br> Ability to compress almost any tubular copper or aluminum part | Strong limitations<br> Cu/Al crimps do not pass cycling tests |
Cost | Optimizes component thicknesses, resulting in weight and cost savings <br>Improved longevity of electrical connections resulting in less down time, less maintenance | Higher thicknesses required<br>More down times and more frequent maintenance due to lower longevity of electrical connections |
Wire Size | Accommodates wide range of wire sizes, in excess of 300mm2 – with no air gaps | Degradation in performance in cables over 70mm2 |
Other Solutions
Are you interested?
Contact us