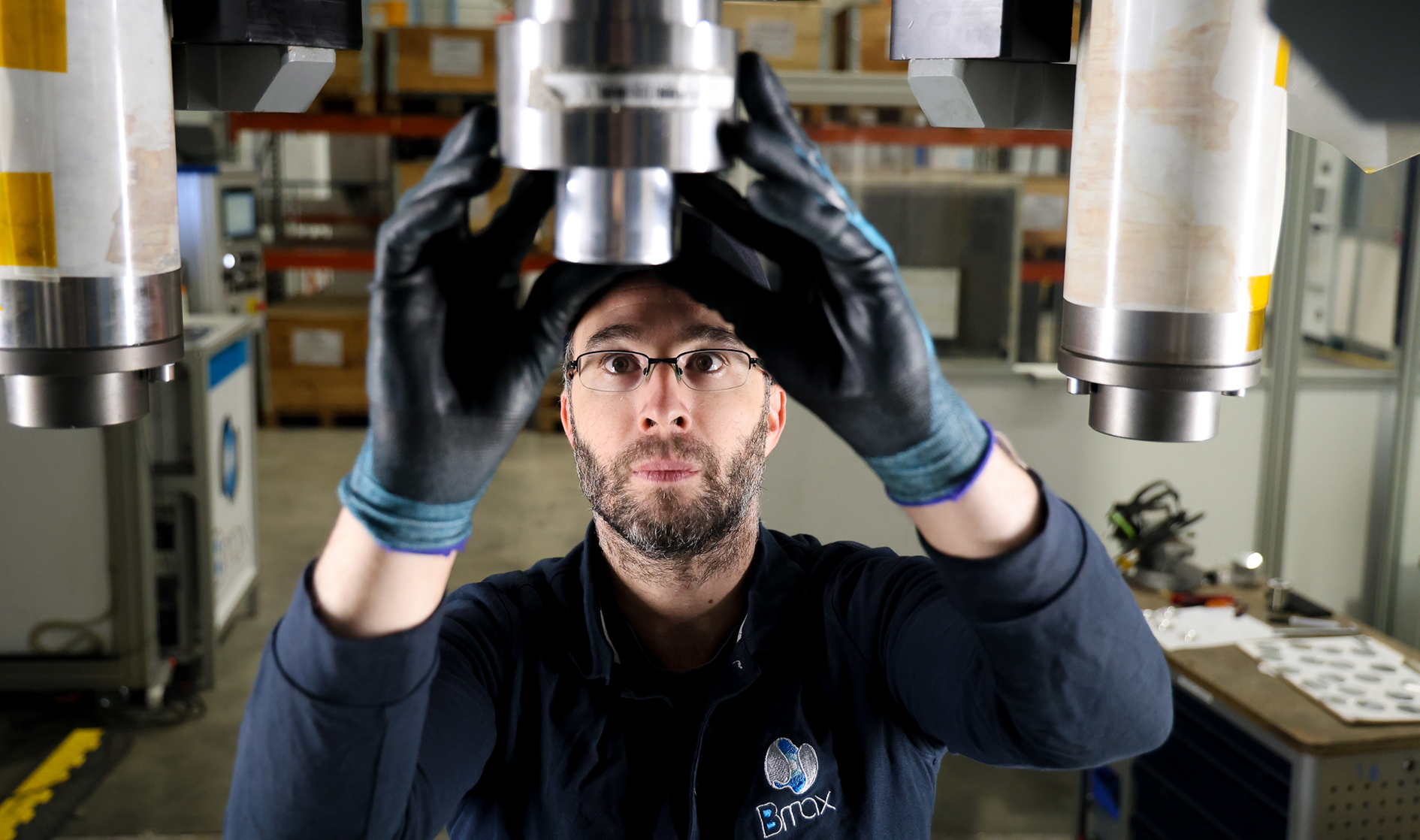
With our innovative, clean, and exceptionally efficient technologies, as well as engineering and design expertise, Bmax empowers its customers to reduce production cycle times, save material, reduce weight and cost, while ensuring the highest level of product performance.
Forming Systems
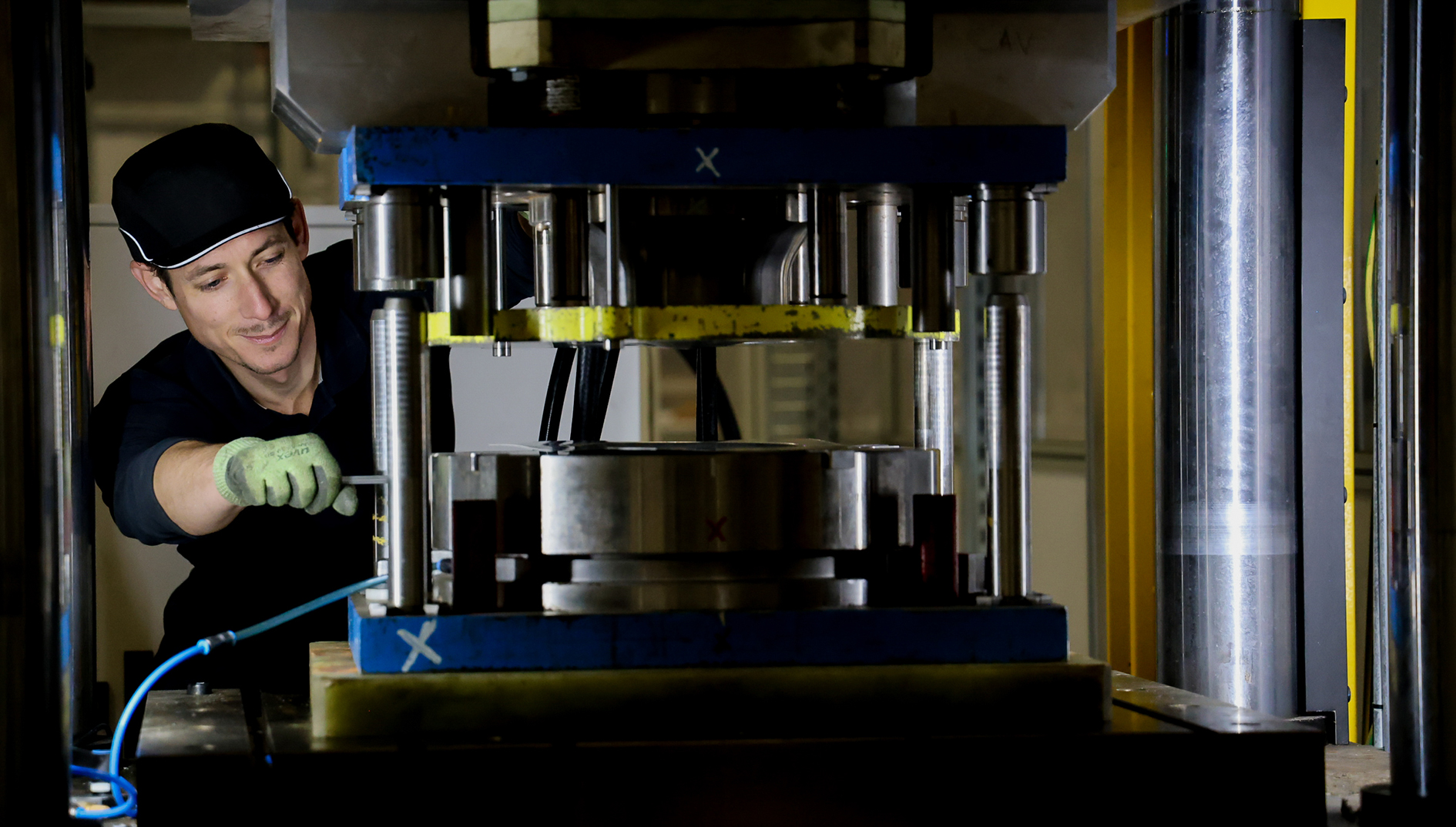
Technical Characteristics
Example Products
Magnetic Pulse Forming: Complex Aerostructure Parts
- Blank dimensions: up to L 1500mm & 3.5 mm thick – depending on material grade and parts geometry
- Material grades: All Aluminum Al 2xxx / Al 5xxx / Al 6xxx / Al 7xxx series
Electro Hydraulic Forming: Complex Engine & Aerostructure Parts
- Overall blank dimensions: up to 800mm x 800mm
Material grades:
- All Aluminum Al 2xxx/ Al 5xxx / Al 6xxx / Al 7xxx series up to 3.5 mm thick
- Steel, Stainless Steel up to 1.6 mm thick
- Cobalt/Nickel-Base alloys up to 1.6 mm thick
- Other material/thickness on demand
Security, health & safety
- No need for manual rework as no more springback to correct
- Embedded with the highest level of machine security in the market
- CE-certified with the support of an independent certification body
- Fully compliant with applicable regulations, technical standards and directives
Compact, Manual or Semi-automatic Production
- Optimized footprint of the production cell
- Design of the production cell according to PN Dimensions & Quantities
High Repeatability, Low Scrap Rate
- Highly repeatable process: Cpk>2
- No mechanical contact between tooling and parts
- Extremely low variations of magnetic pulses
- Typical scrap rate < 0.1%
Process Monitoring
- Fully integrated Process Monitoring System with real time data acquisition & recording
Easy to Operate & Maintain
- Easy to install on a standard Hydraulic Press
- User-friendly HMI
- Easy access to tooling
- Secured access doors to perform maintenance operations
- Remote assistance/maintenance capability
- Optional diagnosis function
Environmentally-friendly
- Low electrical power consumption
- Less forming operations and less annealing steps
- Lower raw material consumption
Products manufactured by our systems
Premium Technology
Electro-Hydraulic Forming | Conventional Forming | |
Number of Tools | 2 | 5 |
Number of Forming Steps | 1 stamping + 1 EHF = 2 | 5 Stampings |
Intermediate Thermal Treatments | 1 | 2 |
Residual Internal Constraints | None No springback – No rework Parts geometrically compliant after EHF | High Springback 100% manual rework needed |
Scrap Rate | < 0.1% | 20-25 % |
Forming Quality & Aspect | Excellent quality & aesthetic <br>Very low thickness reduction <br>Even material distribution | Important thickness reduction<br>Uneven material distribution |
Serial Manufacturing Time | 3.5 hours/part | 13-15 hours/part |
Other Solutions
Are you interested?
Contact us