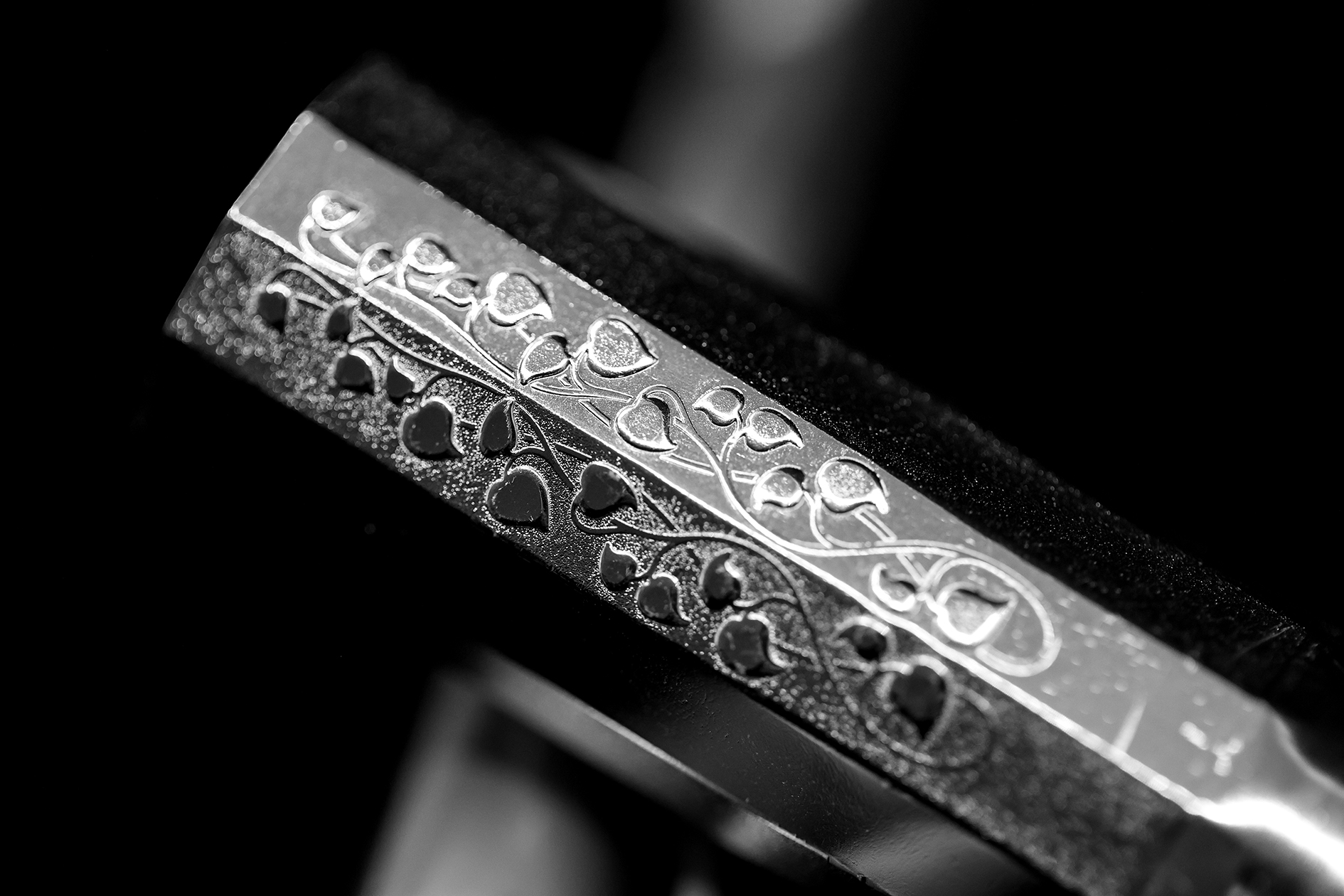
Die Schockwelle im Wasser beschleunigt das Werkstück und versetzt es beim Aufprall auf die Matrize in einen zähelastischen Zustand, wodurch komplexe Formen bei hohen Geschwindigkeiten und kalten Temperaturen geformt werden können. All dies geschieht in weniger als einer Millisekunde. Die gesamte Zykluszeit liegt innerhalb von Sekunden, einschließlich der Ladezeit der Anlage.
Mit diesem Verfahren können Komponenten bis zu einer Größe von einigen Quadratmetern geformt werden. Eine Reihe von Elektroden kann über ein großes Werkstück gelegt werden, was eine Druckverteilung entsprechend der Topologie des Produktes ermöglicht, wobei eine einseitige Matrize verwendet wird, um komplexe Formen und feine Details zu erzeugen.
EHF-Vorteile
Leistungsfähige Produkte
- Deutlich erhöhte Umformbarkeit von Metallen und gleichmäßige Materialverteilung
- Reduzierung der Rückfederung
- Komplexe Gravuren und scharfe Linien/Kanten können leicht geformt werden
- Extrem gute Leistungsfähigkeit beim Kalibrieren von Komponenten
- Hochwertige Oberflächengüte der Komponenten
Umweltfreundliches und sauberes Verfahren
- geringer Energieverbrauch
- geringer Wasserverbrauch in geschlossenen Kreisläufen
Prozessleistung
- Ein einstufiges, extrem schnelles Verfahren
- Es wird nur eine einzige einseitige Matrize benötigt (1 EHF-Anlage kann eine schwere 5-Stufen-Pressenanlage ersetzen)
- Höhere Umformbarkeit (hohe Verformungsgeschwindigkeit)
- Geringere Gefahr von Rissen aufgrund von Reibung, da kein Kontakt zwischen Werkzeug und Werkstück entsteht
- Kann mit jeder anderen Umformtechnik kombiniert werden
- Ermöglicht das Formen von Werkstücken bis zu einer Größe von einigen Quadratmetern
- Formung von männlichen und weiblichen Formen (negative und positive)
- Die Anlage beansprucht eine kleine Stellfläche
EHF System
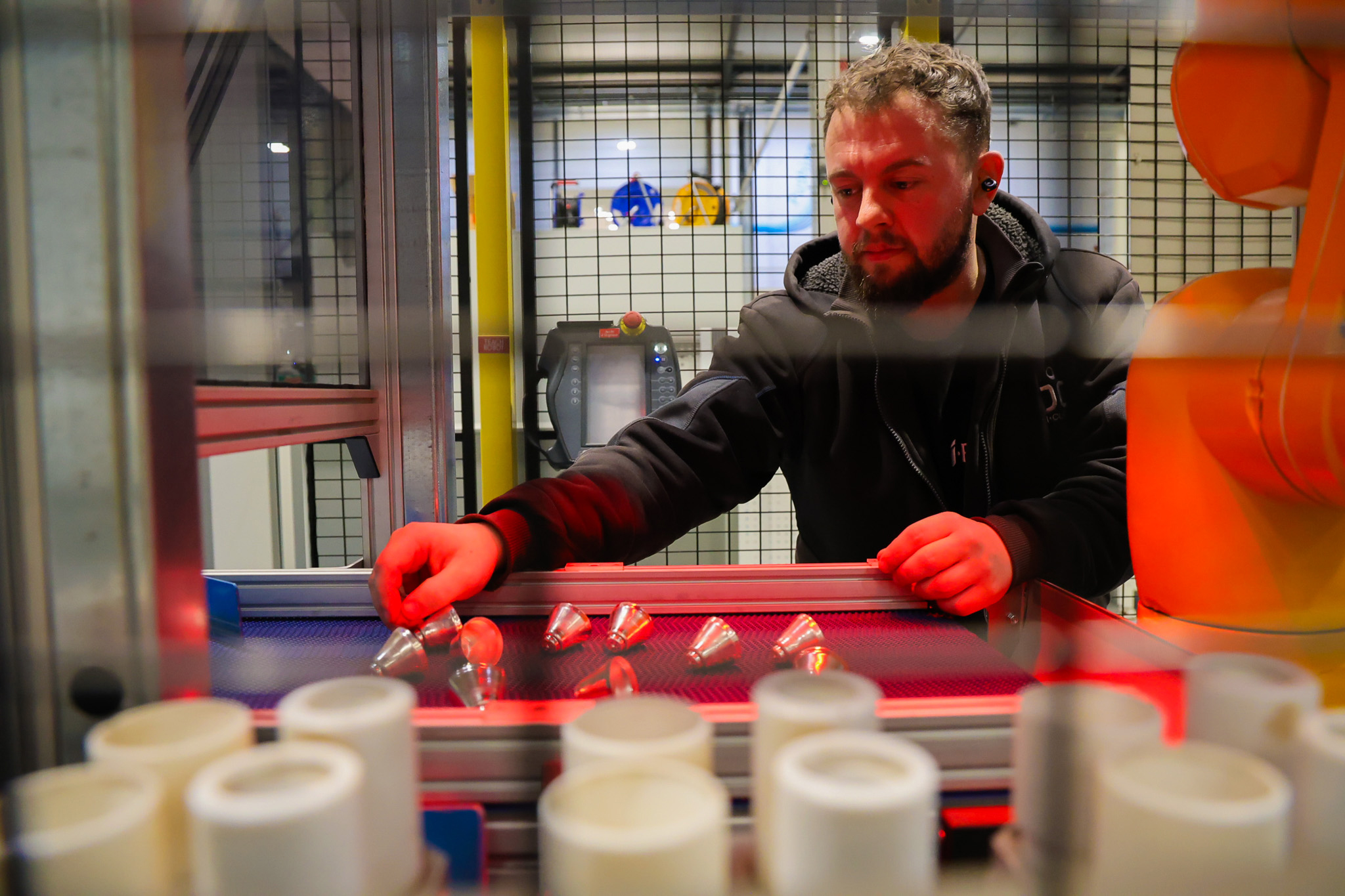
- Up to 700,000 parts/year in 3 shifts
- Fully automatic operation
- Quick change over
- Perfume caps: up to 50 mm in diameter, 80 mm in length
- Lipstick bodies: up to 50 mm in diameter, 80 mm in length
- Decorative lids: up to 70mm in diameter
- Materials: aluminum up to 1.2 mm thick – other materials and thicknesses possible upon request
- Cell size: 2000mm*5300mm*2250mm (h)
- Including: pulse generator, forming cell, water unit, master unit, electrical cabinet, part conveyor
Electrical consumption: less than conventional system